СЛОЖНОСТИ ПРЕДПРИЯТИЙ, СВЯЗАННЫЕ С ИСПОЛЬЗОВАНИЕМ СМАЗОЧНЫХ МАТЕРИАЛОВ
Проводя более 4000 ч в год на предприятиях различных отраслей промышленности, мы наблюдаем похожие сложности.
СЛОЖНОСТИ ВЫБОРА
Выбирать нужно не только марку масла, но и интервал замены. А он зависит от узла, от самого масла, от условий эксплуатации, которые на каждом предприятии свои, от принятых графиков ТО, от состояния техники. Мониторинг помогает определять оптимальные интервалы, чтобы не переплачивать за ГСМ, при этом сохранять ресурс узлов техники.
НЕИСПРАВНОСТИ, ПРИВОДЯЩИЕ К ПРОСТОЯМ
Система мониторинга масла на предприятии позволяет увидеть на ранней стадии неисправности техники и принять меры до того, как они привели к серьезным поломкам.
ВЛИЯНИЕ ВНЕШНИХ ФАКТОРОВ
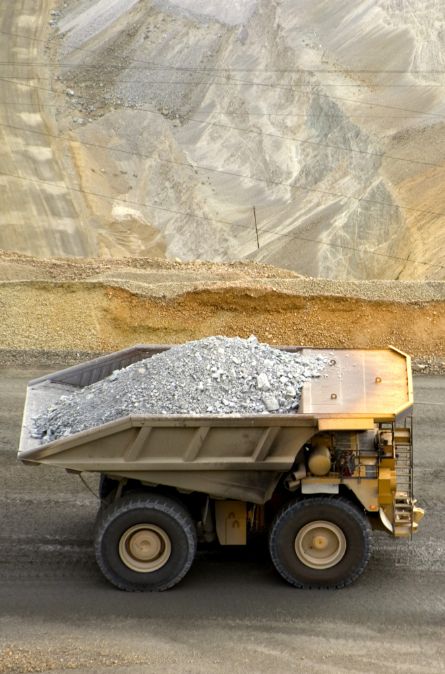
В последние 10 лет практики мониторинга состояния масла активно внедрялись на многих предприятиях, прежде всего в энергетике, горной добыче и промышленном производстве. Предприятия пользуются услугами независимых лабораторий или организуют собственные лаборатории. При этом использовать ценнейший по своей информативности инструмент мониторинга получается далеко не у всех.
ДАЖЕ ВНЕДРИВ ПРОГРАММУ МОНИТОРИНГА, БОЛЕЕ 60% ПРЕДПРИЯТИЙ НЕ ПОЛУЧАЮТ ОЖИДАЕМОГО ЭФФЕКТА. ПОЧЕМУ?
1
Мониторинг работает на сокращение простоев и ремонтов только если правильно сформулированы цели и задачи, назначены ответственные сотрудники, есть быстрая реакция: принимаются корректирующие действия при обнаружении проблем.
2
3
Лаборатории, проводящие анализ, дают общие комментарии по состоянию масла, но они не находятся на предприятии, не знают особенности работы конкретной техники, не ведут историю изменения ее состояния. Чтобы считать максимум информации с каждого анализа, требуется либо специальное обучение механиков, либо привлечение сторонних экспертов.
4
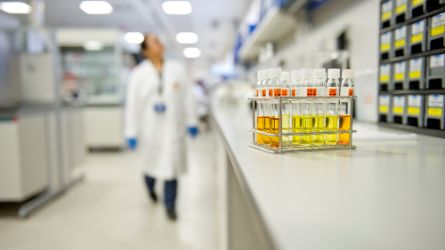
ЧТО МЫ МОЖЕМ СДЕЛАТЬ ДЛЯ ВАС
Многие предприятия бесконечно откладывают задачу по организации мониторинга состояния масла. Непонятно, кто за него отвечает. Не знают, с чего начать. Сложно разобраться, когда и как часто отбирать пробы, куда девать анализы и что за циферки выдает лаборатория. Как от этих циферок перейти к практическим шагам, чтобы стало меншь ремонтов и простоев.